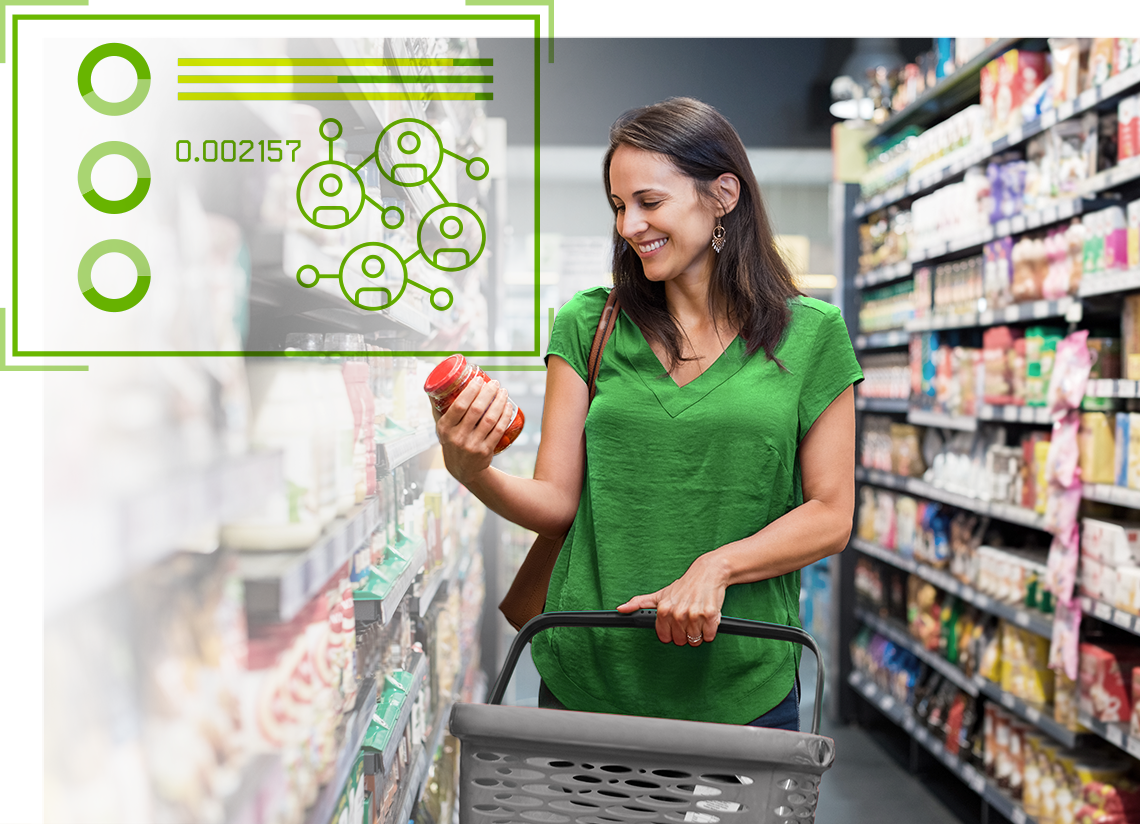
You are looking for individual technical solutions at the highest level of quality?
- A wide range of industries & applications
- Flexible packaging for food and pharmaceutical products
- Barrier coatings on paper packaging
- Lacquering on aluminium foils
- Among other things, functional TopCoat coatings can be applied in various combinations and with corresponding primer / or release coatings:
- Acrylic adhesive coating
- Low temperature seal (LTS) coating
- PolyVinyliDene Chloride (PVDC) barrier coating
- Polyvinyl alcohol (PVOH) coating
- Other customer- & product-specific coating requirements.
- A wide range of web widths and web speeds
- from 300 mm up to more than 3.000 mm,
- from 1 m/min up to 1200 m/min.
PACKAGING
For more than 70 years we support our customers in the development and implementation of individual technical solutions in the field of Coating and Converting, also in the paper finishing – from the conception via detailed tests in our laboratories, the manufacturing and assembly up to the modifications of existing lines.
More than 70 different coating processes which we can also apply in our laboratories form the basis for designing optimal processes that focus on maximum reliability, precision and the avoidance of rejects and are designed for the industrial 24/7 continuous use.
An efficient, energy saving and pinpoint drying is an essential part of the coating lines. Thermal drying processes with lowest tolerances, also supported by IR technology and remoistening, form the basis for products at the highest level of quality.
We know the high demands on technology and process. Polytype Converting® is specialized in meeting your quality expectations 100 per cent. We can provide complete turnkey packages from a single source as well as integration solutions.
COATING
More than 70 different coating processes which we can also apply in our laboratories form the basis for designing optimal processes that focus on maximum reliability, precision and the avoidance of rejects and are designed for the industrial 24/7 continuous use.
The greatest possible flexibility is ensured by using the 'state-of-the-art' trolley technology. When changing products, you benefit from versatile coating techniques at the same coating and lacquering station in the line with quick-change coating modules within the different trolleys.
Here, our AGS® and PGS® pressure chamber doctor system is one of the key technologies in the coating of packaging materials which allows thin uniform and smooth surfaces for functional TopCoats on the substrates. At the same time, it reliably prevents air pockets at the coating point, to achieve the highest possible transparent coating quality.
Another key technology for film coating in the production of flexible packaging solutions is the semi-flexo coating process with vertical nip-feed technology for processing low- to high-viscosity coating media at a wide range of coating weights without the need for roll changes.
Exemplary coating technologies:
- Reverse engraving with pressure chamber doctor (AGS®, PGS®)
- Engraving application – gravure printing / forward / reverse / direct / offset
- Multi roll coater
- Reverse roll coater
- Comma bar (with deflection compensation)
- Slot die coating
- Hot melt coating
- Smooth roll systems with nip dosing incl. specific roll arrangement with different feeding systems
DRYING
An efficient, energy saving and pinpoint drying is an essential part of the coating lines. Thermal drying processes with optimum heat transfer and lowest tolerances, also supported by IR technology, UV- and electron beam curing, form the basis for products at the highest level of quality. Remoistening with steam or water makes it possible to get the moisture that escaped during the drying process back into the paper. This is necessary for the paper web to have a perfect flatness for further processing.
Precise simulations of the drying process, if necessary, supplemented by tests in our technical competence centers – both in Switzerland and Germany - ensure the precise design of the dryers for your products. Uniform drying results that are gentle on the product are ensured over the entire width and length.
A wide variety of dryer and nozzle concepts are realized in all performance and size classes - from nozzle-type air recirculation dryers and cleanroom dryers to floatation dryers with special floatation nozzle technology. Different temperatures above and below the paper web and large recirculating air volumes are also possible. The web guiding is carried out either by floating nozzles, Vacutex® or with idler rollers. All nozzle variants can also be integrated in our Speed-Star® drying systems, which ensure absolute uniformity of the drying processes thanks to their patented air circulation system.
The moisture of paper webs can also be measured in the dryer to effectively prevent over-drying.
You can always rely on the performance of your lines: You achieve high effectiveness through state-of-the-art high-performance components with gentle web transport at the same time - even with low web tensions. Scratching sensitive material webs in the dryer is efficiently avoided.
With working widths from 300 to 3,000 millimeters, all industrial production speeds are possible. In addition, dryers from Polytype Converting® offer good accessibility and are easy to clean.
You are free to determine the energy source of your drying lines when placing the order. In many factories, gas is the preferred energy source. Oil, steam or electric heating systems are also frequently used for heating. The exhaust air produced in the process can be used for energy recovery by a specially calculated system of heat exchangers and is thus part of the CO2 reduction process of your company.
examplary drying technologies:
- Floating dryer with equal or different temperatures above and below the coated web
- Roller dryer with driven idler rolls and upper impingement drying nozzles
- Vacutex® nozzle system with integrated smooth-running and free-running rollers
- External and internal recirculation
- Recirculating air cooling zones
- Speed-Star® recirculation system
- Easy Clean® for easy cleaning
WINDING
Outstanding products require the highest winding quality. Polytype Converting® ensures this winding quality for a wide range of materials, not only for papers, but also for multi-layer laminates, for example. This is achieved, among other things, by programmable and precisely adjustable web tensions and uniform contact pressure forces. The possibility of splicing from both winding directions gives you maximum flexibility. The processing of 3“ and 6“ cores with winding shaft or without axle, is also part of our standard.
Right from the start, we focus on the greatest possible material protection when designing your lines: for the lowest possible load on your products and minimum losses.
With working widths of 300 to 3,000 millimeters and roll diameters of up to 1,800 millimeters and roll weights of up to 5,000 kg, production speeds of up to 1,200 m/min have been achieved for Polytype Converting lines on the market.
exemplary winding technologies:
- Turret winders for continuous line operation
- Shaftless winders and winders with winding shaft
- Flying splice devices
- Pneumatic or motorized impact knife
- Circulating knife chain, rotary knife, lay-on without wrapping (rewinder)
- Residual length optimization (unwinder)
- Automatic loading and unloading
- Contact and circumferential rewinder for surface/tension-sensitive papers and films
TREATING
Perfect coating results for demanding packaging materials require substrates that have been optimally pre-treated for the application.
Since many substrate surfaces of metallized as well as film materials for packaging applications are often hydrophobic, which makes adhesion with a coating solution difficult, the surfaces must be activated to increase the surface tension of the web to be coated or also the web to be laminated before the respective process step.
For this purpose, Polytype Converting® integrates plasma or corona treatment processes.
Likewise, soft edges of the film webs, such as "flutter edges" and an uneven transverse web profile due to thermal stresses, are frequent challenges in the processing of film materials.
With the Polytype Converting® thermo stabilization units - as a combination of heating and cooling rollers as well as in combination with additional infrared heating modules which are zone-controlled across the web width - optimum relaxation can be achieved by the relaxation process even for the most difficult film web materials.
In addition, web cleaning devices can be positioned behind the unwinder close to the pretreatment process to ensure perfect dust-free product quality before coating.
Leistungen im Full-Service-Paket
In sechs sorgfältig aufeinander abgestimmten Schritten realisieren wir Ihr individuelles Maschinenbau-Projekt:
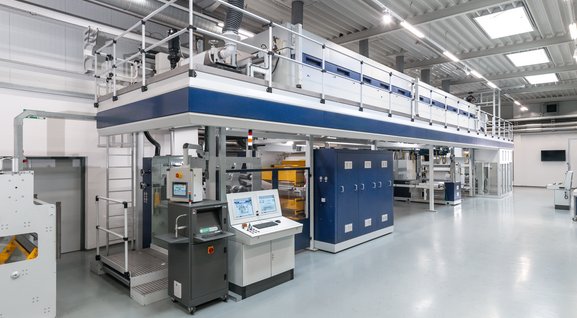